-
Micro Stepper Motor
-
Permanent Magnet Stepper Motor
-
Geared Stepper Motor
-
Linear Stepper Motor
-
Slider Stepper Motor
-
Hybrid Stepper Motor
-
Small DC Gear Motor
-
ROV Thruster Motors
-
Micro Metal Gearmotor
-
Micro Gearbox
-
Position Control Stepper Motor
-
3D Printer Stepper Motor
-
Stepper Motor Driver
-
DC Motor Controller
-
Lead Screw And Nut
-
Andres BlancoThe thruster have arrived correctly. I tested them on the ROV and we are very happy with the result. The epoxy interior finish is very good and the power of the motors in relation to the size is quite good.
-
Gregoire LangeThe cooperation between Changzhou Vic-Tech Motor Tech and our company was just great. Good understanding of our needs, great willing to solve our problems. I recommend !
-
David MoleveltProfessional and clear communication. Order was shipped in time. Counter connectors where added to the shipment. Driver works like we agreed !
-
Buildstorm Private LimitedThe product works as expected, it was packed nicely. Seller responds very quickly and helps in making a buying decision. They are ready to customize the product for you.
-
Ashley GriffinShipment was received very quickly. Product was well protected by packaging. Company rep was cordial and kind. A Plus rating!
Sumax DC 24 - 36V Remote Control Underwater Thruster Motor for Precision Electronic Instrument
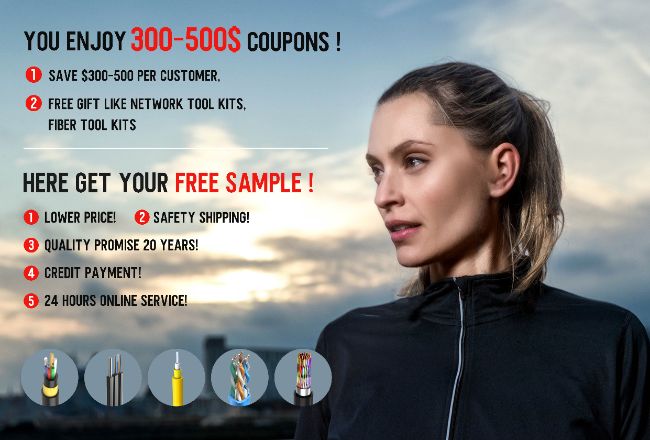
Contact me for free samples and coupons.
Whatsapp:0086 18588475571
Wechat: 0086 18588475571
Skype: sales10@aixton.com
If you have any concern, we provide 24-hour online help.
xProduct Name | Underwater Motor | Model | 2216 |
---|---|---|---|
Voltage | 24 - 36V | Max Power | 150 W |
Speed | 3150 RPM | KV Value | 350 |
Highlight | 24V Underwater Thruster Motor,Remote Control Underwater Thruster Motor,sumax underwater electric thruster motor |
Sumax DC 2216 24V underwater remote control robot drone thruster motor
As one of earliest manufacturers developing underwater motor in China, we have ripe experience on designing and producing underwater products (we also provide OEM service), and reliable experimental data.
At the same time, we developed underwater motor potting technique, which protects stator from water, we have obtained National utility model patent certificate.
Our 2216 motors receives very decent feedback from customers around the world, and our customers are quite impressed by its performance.
If your company demands developing and producing underwater products, please feel free to contact us.
Main Features:
Used for RC Boats, RC Submarines, Underwater ROV, Water Scooters, other diving electronic device
Can be soaked into water without any functional problem up to 200m depth.
Parameter:
KV Value | 350 | Voltage | 3s/4s |
Max Current(A) | 10 | Motor Core | Japanese Kawasaki Silicone Steel (Thicknes0.2mm) |
Max Power(W) | 150 | Magnet | NdFeB N48H |
Weight(g) | 74 | Slot & Pole Distribution | 12N14P |
Shaft Diameter(mm) | 3 | Bearing | EZO Stainless Steel |
External Size(mm) | 28*48.5 | Appearance Craft | Hard Anodizing |
1.Wiring method
irst of al, the motor, power supply and EsC should be selected accurately according to the load and use conditions, thepower supply voltage is too high is likely to cause damage to the motor and Esc, the power supply discharge power isnsufficient to allow the motor to reach the rated power and affect the use of the effect. ESC selection should also bematched with the rated voltage of the motor, Motor installation screws should not be too long, so as not to damage themotor coil. Before wiring, for safety, please remove the motor load, first connect the ESC and motor three leads (threeeads can be switched two to change the direction of the motor), and then connect the EsC signal line, pay attention tothe signal line wiring order, do not connect the reverse. finally connect the DC power supply, positive and negativebolarity can not be reversed, most of the market ESCs have reverse protection, no reverse protection ESCs in the powersupply positive and negative polarity will have the risk of burning.
2.Throttle travel calibration.
When using ESC for the first time, or change the PWM siqnal source, or use the throttle signal out of calibration for along time, you need to calibrate the throttle travel.
Design layout: